Exploring new opportunities with third generation advanced high strength steel
WarP-AHSS: Warm Press-Formed Zinc-Coated Third Generation Advanced High Strength Steels with High Crash and Corrosion Resistance and Minimized Microcracking
Why WarP-AHSS?
The motivation of WarP-AHSS project is to solve the drawbacks associated with the conventional C-Mn-B hot stamping steels by employing the concept of zinc-coated “medium manganese” 3rd generation advanced high strength steel (3G-AHSS).
Steel sheets at automakers are formed in different ways (e.g. cold forming, hot forming, roll forming etc.) for use in car bodies. Hot stamping (or hot forming or hot pressing or hot press forming or press hardening) is one of the forming method for automotive components which is growing rapidly in Europe. Typical candidate alloys for hot stamping steels are C-Mn-B steels such as 22MnB5 grade, which, after hot stamping, can achieve a fully martensitic microstructure with a yield strength (Rp) ~1000 MPa and a tensile strength (Rm) of 1400-1600 MPa. However, there are several major drawbacks of using C-Mn-B steels, as listed here, which are aimed to overcome in the WarP-AHSS project.
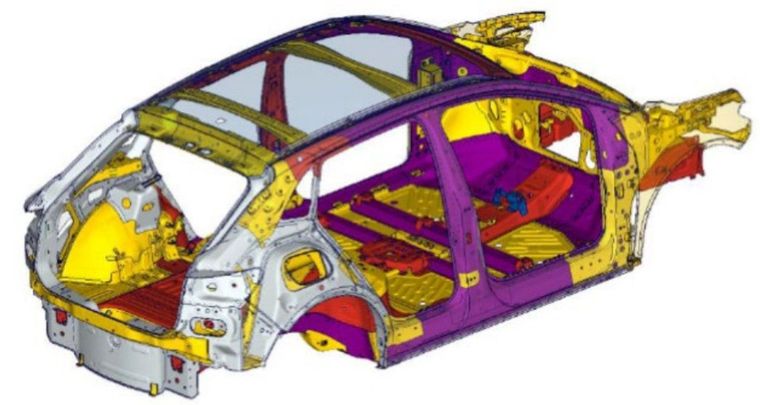
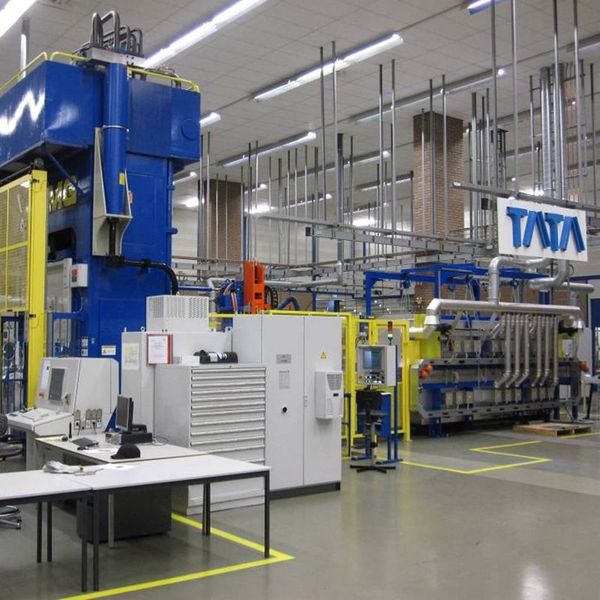
Objectives
In the WarP-AHSS project, it is primarily aimed to develop the following two types of Zn-coated “warm pressed” medium manganese steel products that will use significantly lower processing temperatures enabling the use of Zn-coated sheet steels for warm stamping parts and avoid the occurrence of liquid metal embrittlement (LME) and other coating and surface degradations during warm stamping:
1. Intrusion-Resistant Warm Stamping Steel:
with tensile strength (Rm) similar to 22MnB5 but higher elongation
2. Energy-Absorbing Warm Stamping Steel: with significantly higher product of Rm x A50 than 22MnB5 and other available ductile hot-press formed steels