Project WarP-AHSS
Motivation
The motivation of WarP-AHSS project is to solve the drawbacks associated with the conventional C-Mn-B hot stamping steels by employing the concept of zinc-coated “medium manganese” 3rd generation advanced high strength steel.
Steel sheets at automakers are formed in different ways (e.g. cold forming, hot forming, roll forming etc.) for use in car bodies. Hot stamping (or hot forming or hot pressing or hot press forming or press hardening) is one of the forming method for automotive components which is growing rapidly in Europe. Typical candidate alloys for hot stamping steels are C-Mn-B steels such as 22MnB5 grade, which, after hot stamping, can achieve a fully martensitic microstructure with a yield strength (Rp) ~1000 MPa and a tensile strength (Rm) of 1400-1600 MPa. However, there are several major drawbacks of using C-Mn-B steels, as listed below, which are aimed to overcome in the WarP-AHSS project.
- The total elongation (A) of 22MnB5 is relatively low, typically about 6%. Although due to the ultrahigh strength of 1400-1600 MPa, 22MnB5 is suitable for intrusion resistance (e.g. in a B-pillar), it behaves poorly in crash energy absorption. Therefore, steels with reduced carbon content like Ductibor 1300, B1200, Ductibor 1000 or Ductibor 500 were developed. However, these steels sacrifice strength for more ductility which gives a low value of Rm x A reducing the crash energy absorption.
- Typically, 22MnB5 is reheated to 900-950°C to achieve a full austenitization and then transferred to the press for hot stamping also at quite high temperatures (700-800°C) to avoid proeutectoid ferrite formation. These high process temperatures lead to higher energy consumption.
- Besides higher energy consumption, these high processing temperatures leads to degradation of the coating of precoated sheets. In particular, with the use of Zn-precoated sheets several problems arise such as liquid metal embrittlement (LME) and microcracking during direct hot stamping (and also during resistance spot welding) and therefore usually other types of coatings (typically Al-Si based) are employed. However, when comparing the corrosion protection of these different types of coatings, the Al-Si based coatings are inferior to Zn-based coatings because they offer only a barrier protection. The electrochemical potential of the resulting Al-Si-Fe layer is so close to the potential of the base steel that it cannot provide enough cathodic protection. In contrast, Zn-rich layers offer an additional cathodic protection, also protecting uncoated edges due to cutting of the coated sheets.
- Furthermore, Al-Si based coatings form Al-Si-Fe containing hard intermetallic particles due to reheating at high temperatures which are brittle and cause wear and pollution of stamping dies (called “galling”) which requires frequent costly maintenance and changing of dies.
- Also, hot stamped Al-Si coated 22MnB5 steels often require sand blasting, involving additional costs and installation, to remove the surface oxides formed at high reheating temperatures before they can be welded for assembling into the car body.
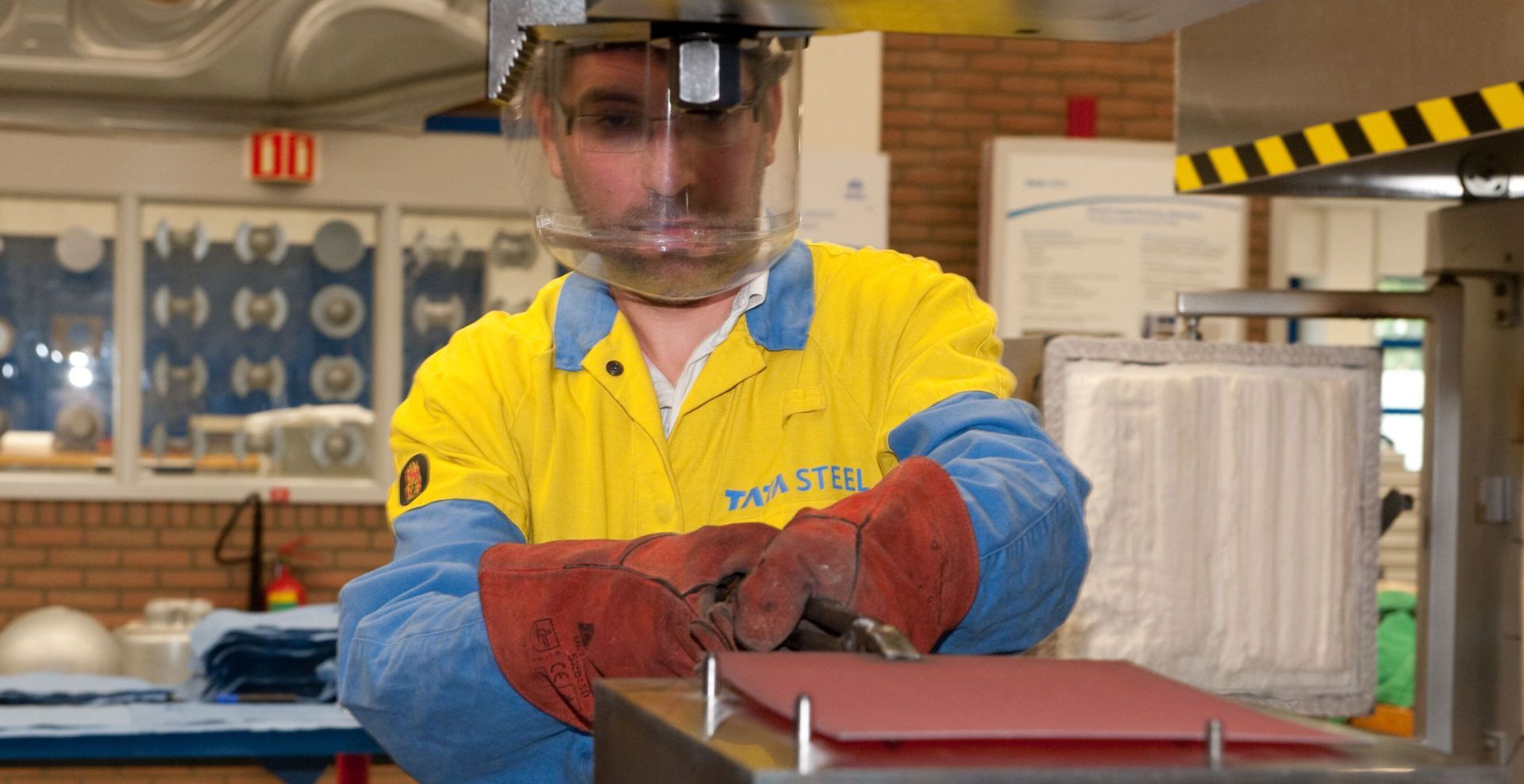
Mission
In the WarP-AHSS project, key players from steel industry & automotive industry, as well as from academia and research community in Europe have assembled to develop a new product technology in the area of hot press forming. Specifically, this project will develop end-to-end processing of warm press-formed parts for lightweight automobiles from zinc-coated novel ultrahigh strength Medium Manganese Steels (MMnS). Besides ultrahigh strength, the ductility, energy absorption capacity and the corrosion resistance of warm-pressed parts will also improve compared to conventional AlSi-coated hot-pressed boron steel parts. The MMnS will enable to significantly reduce the reheating and warm press-forming temperatures, making the process greener and energy-efficient, and allowing the use of zinc-coated sheets without liquid metal embrittlement-induced micro-cracking during warm-pressing. Prototype parts will be produced by warm-pressing of zinc-coated MMnS and mechanical properties, crashworthiness, corrosion resistance, hydrogen embrittlement and weldability will be investigated.