Objective
Primary Objective
In the WarP-AHSS project, it is aimed to develop the following two types of Zn-coated “warm pressed” medium manganese steel products that will use significantly lower processing temperatures enabling the use of Zn-coated sheet steels for warm stamping parts and avoid the occurrence of liquid metal embrittlement (LME) and other coating and surface degradations during warm stamping:
1. Intrusion-Resistant Warm Stamping Steel: with tensile strength (Rm) similar to 22MnB5 but higher elongation
2. Energy-Absorbing Warm Stamping Steel: with significantly higher product of Rm x A50 than 22MnB5 and other available ductile hot-press formed steels
Secondary Objective
Apart from the above primary objective of the development of new and improved hot stamping steels, a secondary objective of the project is replacement of cold forming advanced high strength steels (AHSS) in automobiles such as high strength dual-phase steels with ≥980 MPa tensile strength (DP980 grade). Here, the aim is to modify the heat treatment/warm stamping of the energy-absorbing variant of the medium manganese steels (MMnS) to better fulfil the requirements for the mechanical properties of cold forming AHSS. The warm stamping of a zinc-coated MMnS would overcome a lot of effort and problems involved in the cold pressing of high strength steels, such as high pressing forces, high springback and the many forming steps associated with cold stamping process. This project will develop a warm stamping process of zinc-coated MMnS with a major reduction of the number of production steps.
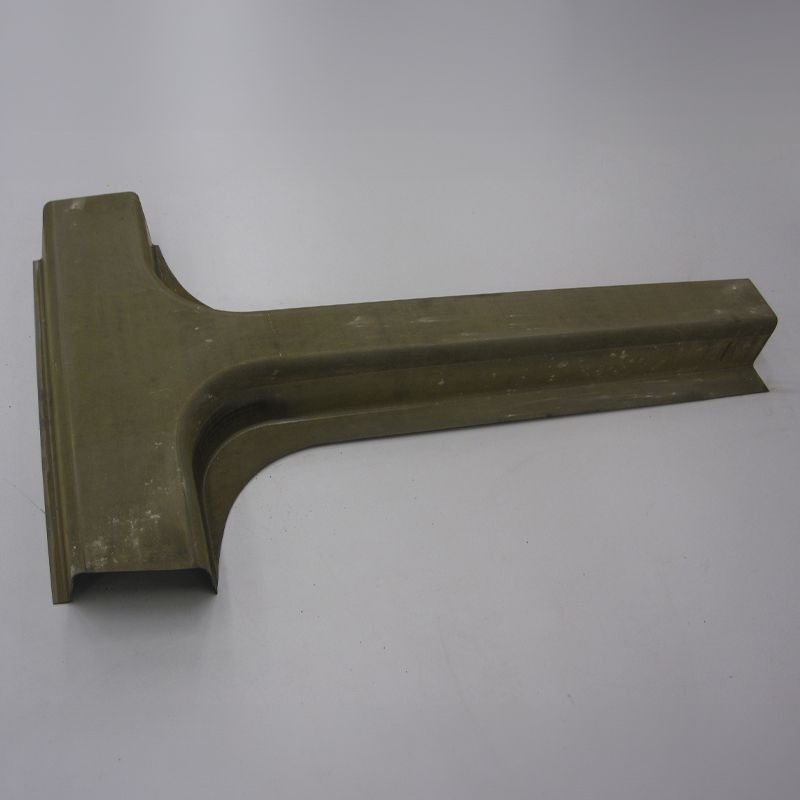
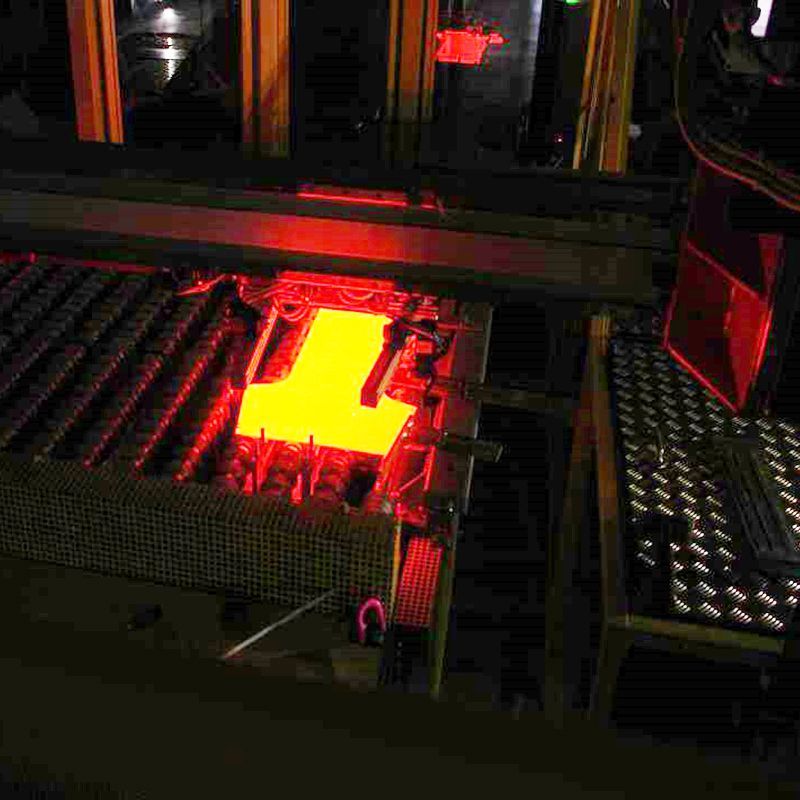
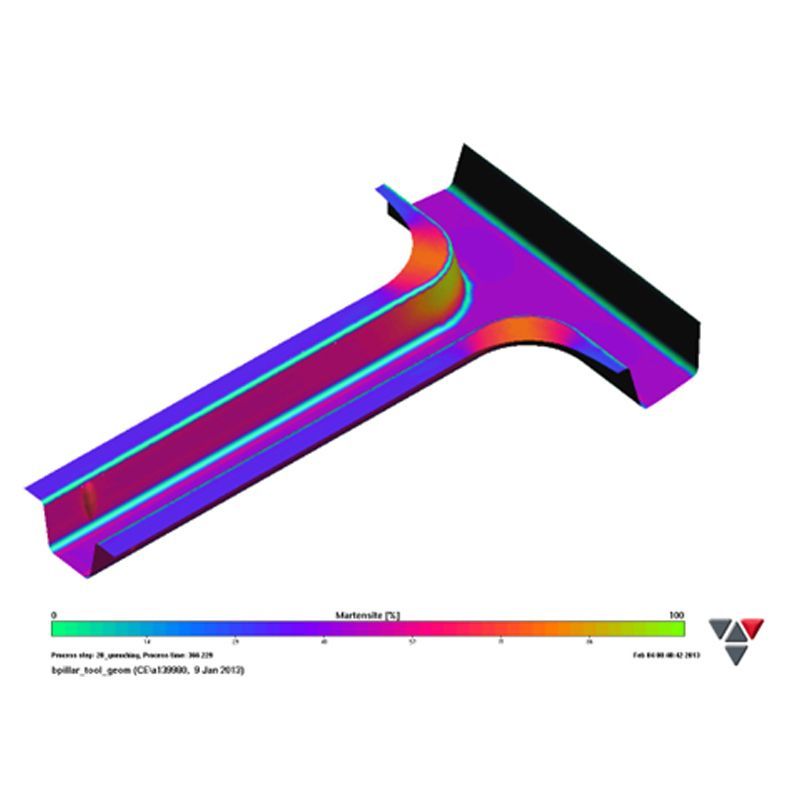
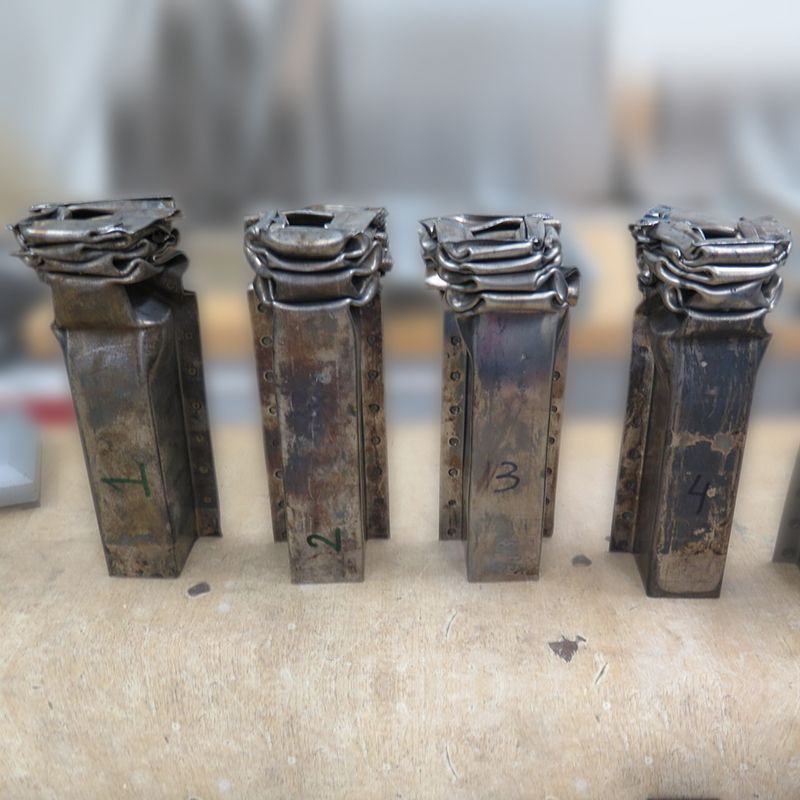
Specific Objectives
From the big-picture objectives described above, a set of specific objectives are also drawn. Related to the current use of C-Mn-B steels (e.g. 22MnB5) in hot stamping and high strength steels in cold forming (e.g. DP980), we aim to improve on/investigate the following specific points:
- The high blank reheating (≥ 900°C) and hot stamping temperatures (≥ 750°C) lead to issues of LME and coating/substrate degradation (microcracking, oxidation and pores) with Zn-coated sheets. Therefore, typically AlSi-coated sheets are used with limited corrosion protection of the final product. Thus, reductions in reheating and hot stamping temperatures by using medium Mn steels which will be developed in this project can facilitate the use of Zn-coating. Additionally, these reduced processing temperatures would reduce energy consumption and accordingly reduce gas consumption and CO2 emission during processing.
- Develop an optimized reheating and warm stamping low-temperature process to avoid LME, minimizing degradation of coating and steel substrate, and optimizing the mechanical properties and corrosion resistance of final warm pressed parts.
- The 22MnB5 after hot stamping has limited residual ductility (≤ 6%). Especially for parts with demands for high crash energy absorption, an increase of the product Rm x A is required to allow further reduction of weight or raise in passenger safety. Our approach is to use Medium Mn Steel (MMnS) concept which allows to achieve high residual ductility due to its microstructure characteristic of a 3G-AHSS (i.e. with retained austenite) that will increase Rm x A.
- Investigate the effects of variation of steel producers’ annealing after cold rolling.
- Produce high quality Zn-coatings for MMnS sheets by hot dip galvanizing (GI) and galvannealing (GA) and study the effects of these coating process parameters. Prototypes of coated sheets will be made to show the results.
- Compare hydrogen sensitivity of warm pressed MMnS (with/without retained austenite) and 22MnB5 with an aim to eliminate/minimize hydrogen embrittlement in the developed MMnS.
- Investigate resistance spot weldability of warm pressed Zn-coated MMnS parts with an aim to minimize weld LME cracking and optimize weld strength.
- Manufacture prototype parts for mechanical testing, including crash tests, comparing with reference grades (22MnB5 and DP980) and finite element modelling (FEM) performance simulations of prototypes.